The result of this lamination was, unexpectedly, inferior to the other hull side. The problem is too much resin left in the laminate. Also there were a few dry spots, I fixed those with more epoxy before the first batch was fully cured and expect a good chemical bond to the rest of the laminate. I think there are several factors leading to this result:
1. Higher temperature in the workshop. The temperature makes a huge difference on the gel-time of the epoxy.
2. Holes in the bag, it took a long time until these were located and fixed. This also lead to more epoxy gelling before adequate vacuum.
3. Huge overlaps of the release film. The worst result is in the bow area, I found huge overlaps of release film here. The release film is perforated, but when two layers overlap the perforations does not align and there is no way for the epoxy to escape.
All the above leads to less distribution of and less escape of excess resin.
This inferior result does not compromise the structure of the hull, it just makes it a bit heavier and with a more uneven surface in the interior. All over I'm happy with the result.
Fixing dry spots:

Hull half overview:

The daggerboard case mold. Raised area for making recess. I will make a test infusion with gelcoat first layer to the mold. If this works I will probably try this with the foils as well.

Anchor locker mold:
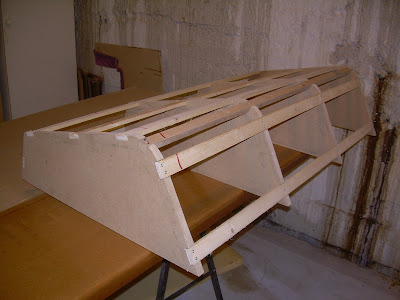
This is to notify the owner of this hat that it has been taken care of to the best of my abilities.